“这条铝锻自动化生产线目前属于行业先进水平,计划四月份实现量产。”2月21日,在金马工业集团铝锻试生产车间,高度自动化的锻造生产线仿佛一座精密的“未来工厂”,智能控制系统实时监测着每一个生产环节,金马集团技术中心副主任张炜逐项介绍着产品性能。
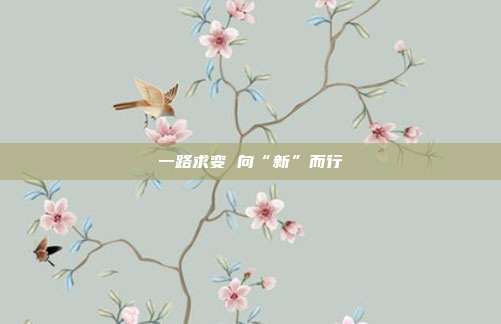
随着工业技术的不断发展,市场对铝合金锻产品的需求逐渐增加,特别是在航空、新能源汽车、轨道交通等行业,铝合金锻产品因其轻质、高强度的特点而得到广泛应用。为了满足市场需求,金马集团紧抓铝锻轻量化生产的市场化风向,投资了新的铝锻车间,从单一的钢锻向铝合金锻造方向发展,为客户提供“钢加铝”的综合服务,企业创新和持续发展能力实现大幅提升。
然而,这条“轻量化”的铝锻生产线背后,不仅是技术创新的成果,更是企业攻坚克难的缩影。如何在轻量化的同时保证产品性能,金马集团专门组建了一支由行业专家组成的研发团队,经过不断的科技创新,最终突破关键技术壁垒,研发出具有自主知识产权的铝合金产品制备工艺,让金马集团成功跻身高端铝合金零部件轻量化领域。
“目前开发的产品主要应用于商用车燃油系统油量控制器、空调压缩机中的涡旋盘,以及乘用车底盘的拉杆、控制臂等。”张炜介绍,从钢材锻造到铝材锻造,在“金马制造”的高质量发展之路上,金马集团始终与市场需求同频共振。
聚焦“专精特新”领域,金马不断调整产业结构,汽车零部件主导产品从2000余个粗加工产品精减到200余个,转向系统、制动系统多个产品的市场占有率世界领先。先后建设了国内首条通孔轴头智能锻造自动线、国产锻造机器人自动生产示范线、多类多轴智能机械加工生产线等,先后研发8000T热模锻、铝合金轻量化等新工艺、新技术在精密关键汽车零部件方面的应用,实现60余个新产品的开发突破。
一旦开启“领跑”状态,就像打开了磁力吸盘。在不断加快商用车转向系统关键零部件全链条制造技术研发和产业化的同时,形成了从锻造、热处理到精加工一体化的综合解决方案,连续开发包括汽车转向、制动、行驶等系统关键零部件产品,其中重型商用车转向机活塞、盘式制动器杠杆等产品国际市场占有率达已超过三分之一,商用车转向机活塞、扇形齿轮轴产品获得国家制造业单项冠军的产品。
绿色,是新时代发展的硬指标,也是金马集团发展的新标志。基于日照大力进行新能源发展的大背景,金马集团还与中国船舶集团风电发展有限公司共同投资建设中船金马日照绿色能源装备制造基地项目,旨在打造以风电主机、主控系统为主的综合性新能源装备制造基地,建设海洋牧场、海上风电、海洋文旅为一体的蓝色海洋经济综合体项目,实现一、二、三产融合发展。这也是金马集团探索“新能源+低碳”模式,发挥风力发电装备在技术研发、智能制造、市场生态建设等方面优势,助力新能源产业应用和推广的重要举措。
从钢锻领域步入铝合金轻量化市场,金马集团用创新与坚持书写了属于自己的故事。金马集团也将继续以技术创新为驱动,以国际化视野为引领,为行业的高质量发展注入新动能。(日照报业全媒体记者 蒋月阳)
版权声明
本文系作者授权念乡人发表,未经许可,不得转载。